Precision In Motion With Exploring Gear Hob Cutters
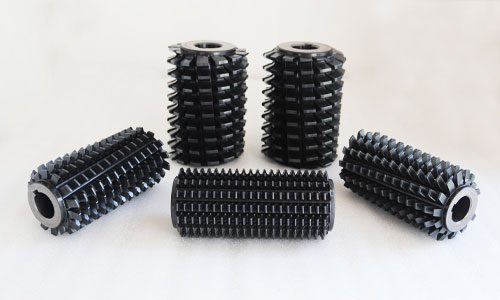
Gear hobbing is known for its quick and adaptable process, essential for gear manufacturing. Every gear hobbing machine uses a rotating cutting hob or tool to generate a specific tooth profile on specific gears as provided through the machine. The accuracy and exactness of gear hobbing make it the perfect method for gear manufacturing.
Gear Hobbing Works process
Every gear hobbing machine has two skew spindles, in which one spindle accommodates the hob and the other places the gear blank. These spindles are placed at an angle relative to each other and greatly depend on the class of gear being manufactured. While the spindles keep at the actual angle, the hobbing machine begins to rotate the shafts at the proper speed ratio that suits the gear type. With shaft rotation, the hob slowly cuts the teeth with the accurate depth into the gear. To enable faster production, gear hob manufacturers can pile multiple blanks on dedicated spindles concurrently, which allows the hob to slit teeth into numerous gears at one time.
Factors Amongst Gear Hobbing and Milling
Gear hobbing and gear milling are two processes that can be used to manufacture gears, although they require different cutting techniques.
- Gear Hobbing
Gear hobbing is mainly a function of generating gear teeth with the help of a helical cutting tool or with the hob. The hob and gear blank are rotated constantly until dedicated gear teeth are slit into a blank. The super speed of this technique makes it perfect for more extensive production to run.
- Gear Milling
The gear milling method uses a cutter(form cutter) that forces axially to create a gear tooth at the right length and depth. Every time the tooth is slit, the gear hob cutters are withdrawn to entitle the gear blank to turn to the next position. After the blank rotation, the form cutter slices the next tooth. This process resumes throughout until all teeth are cut to the blank. This method is slower, which makes it a low-production method.
How to pick a Gear Cutter
Involute gear cutter is the best option to make a small quantity of gear. This type of gear cutter is needed to replace broken gear. This kind of gear cutter works excellently in mills. Sometimes, it allows you to extend the capabilities of machines.
To utilise an involute gear cutter properly, you must understand the pressure angle, pitch (or module) and the number of teeth of the gearbox you are attempting to produce. The cutter will be particular about the pitch and pressure angle thus they must match exactly. Each device cutter is also only appropriate for cutting a range of tooth counts; thus it requires eight distinct cutters to manufacture every gear between 12 teeth to a rack (“infinite” teeth).
Just as manufacturers can utilise a variety of angles, speeds, and procedures to customise the process, an extensive range of hobbing machines are available. Most hobbing machines specialise in specific uses.